The contamination of water and/or poisoning of employees with hazardous substances through the fault of the employer or a fire is a scenario that cannot be ruled out in any location, not only those strictly related to industry. One way to reduce the risks associated with storing chemicals and hazardous substances is to purchase the right cupboard.
There are plenty of substances that pose a threat to the environment. Sometimes they have to be stored indoors, e.g. in laboratories, service centres or paint shops. Collecting hazardous materials in jars, cans or boxes, for example, and storing them in conventional cupboards should not be considered at all. Especially since the storage of such substances is strictly regulated by the European Standard EN 14470-1.
A solution to reduce the risk of leakage and contamination is hazardous material cabinets, which at the same time minimise the risk of fire from the stored product and prevent the escape of harmful vapours into the environment. In addition, the cabinets give employees the feeling of performing their work duties in a more comfortable and safer environment.
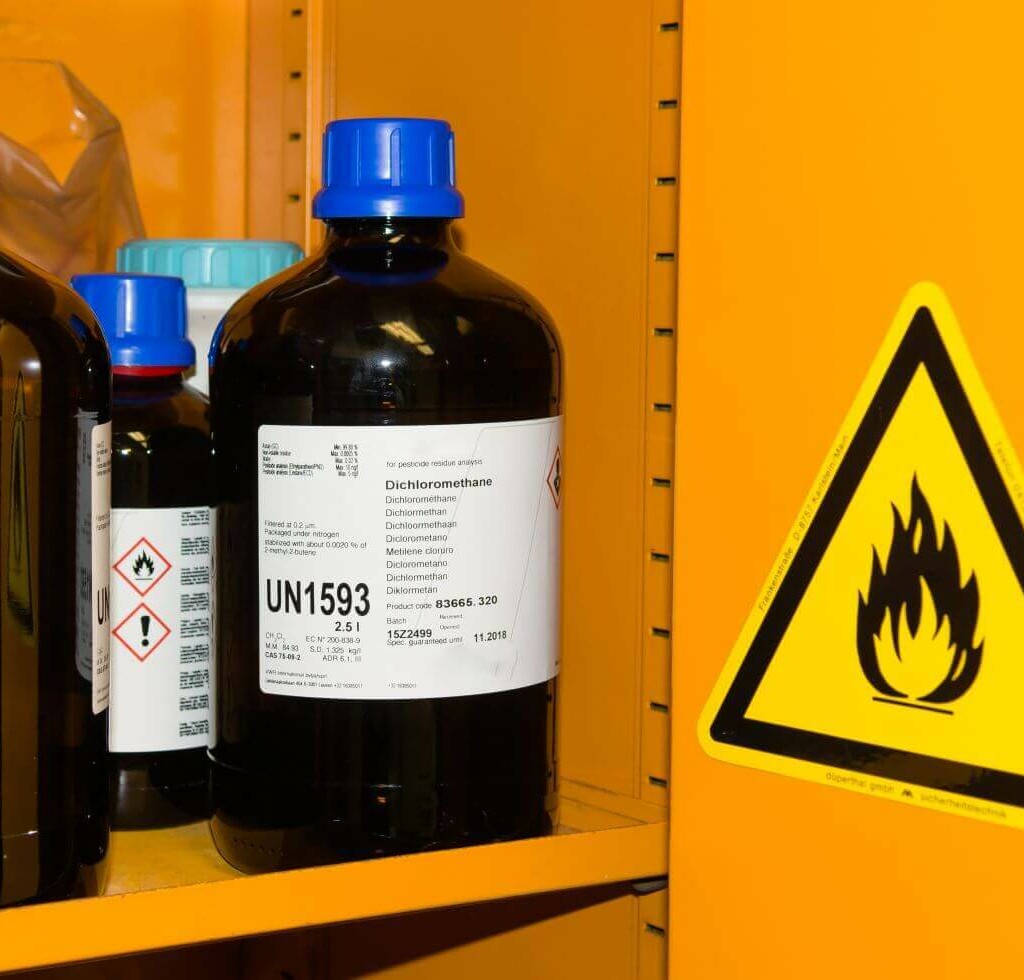
Leakage under control
Bath shelves are standard in hazardous material cupboards. Usually one to three, but the exact number depends on the size of the specific model. Manufacturers also make sure that the shelves can prevent any possible leakage of liquid outside the cupboard. In selected units, the shelves have a load capacity of 50 kilograms and a capacity of 20 litres. Typically, the bottom trays have a larger capacity, such as 30 litres. They are made of sheet steel, usually 3 millimetres thick.
Safely behind the door
Ecological storage cupboards are usually fitted with a key lock. This ensures that hazardous substances cannot fall into the wrong hands. Manufacturers install single or double doors. The former usually open to the right and the opening angle can be more than 90 degrees. In good models the doors are equipped with a system of automatic locking of the cabinet in the event of a fire. In the cheapest models ventilation holes are drilled in the upper and lower part of the door. In order to make sure that the vapours which are emitted do not cause a possible increase in the concentration of dangerous vapours, which could occur if only gravitational ventilation is used, it is necessary to install a special module in the cupboard, which by forcing air circulation in the cupboard will remove the vapours which are produced to the ventilation system.
The ecological storage cupboard is the optimum solution for workplaces where hazardous substances are used. It is not only an investment to protect nature and the environment. Everyone benefits from using this solution: the employees – first and foremost the feeling of comfort and safety; the employers – compliance with health and safety requirements and applicable standards.
Read also: Green cabinets: safety and environmental protection in business